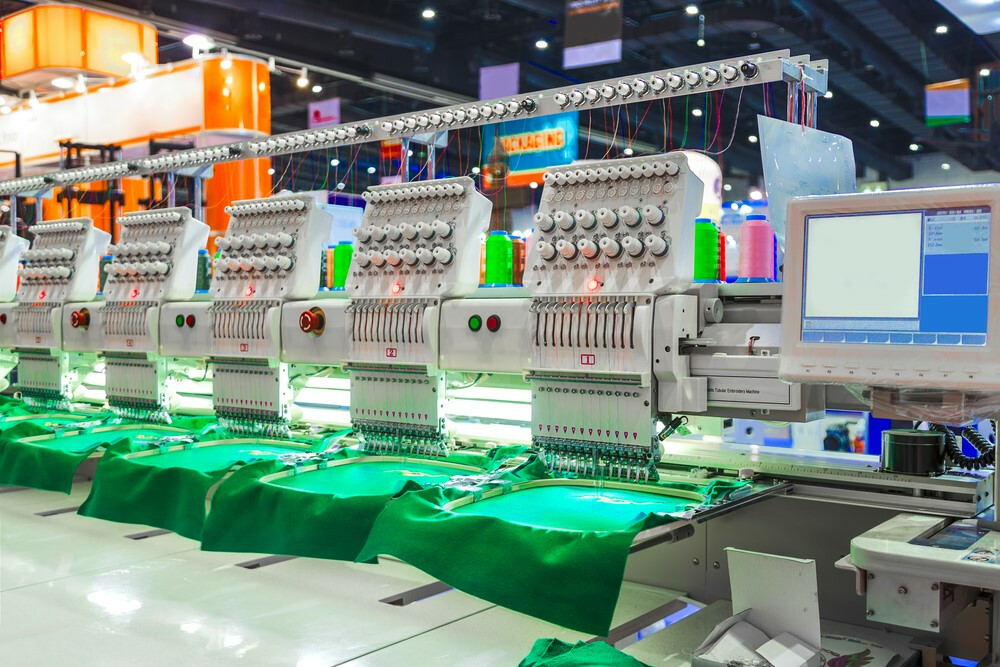
Digitizing: The Secret to Successful Patches
Can You Dig-it? Digitizing is the key to custom embroidered patch production.
You might have noticed we talk quite a bit about patches around here. We’ve considered the merits of different patch types, the best patch styles, how to make patches stand out.
We’ve discussed lots of things about patches, including how they’re made. One thing we haven’t talked about is one very important step in the process of making custom patches – digitizing.
- The Hidden Step
You probably don’t think about digitizing when you’re ordering. It’s the hidden step in producing your patches. It’s a vital component of making sure that your patches turn out exactly the way you want them to.
Simply put, digitizing is the process of turning your patch design into a digital file. Specifically, it means turning your artwork into a file that a computer-controlled embroidery machine can translate into stitching.
It’s not as easy as it sounds. When we receive your design in whatever format you send it to us, we can’t just program that file into an embroidery machine. The machine can’t read it. And it’s not just a simple matter of conversion. The digitizing process really is a blend of both art and science.
What Does a Digitizer Do?
To begin with, most commercial embroidery machine manufacturers require their machines to use their own proprietary software file types. You can’t just digitize a file in a format for Machine A and expect it to work with Machine B. So the digitizer must know what brand of machine the factory uses.
Details are important. The person doing the digitizing uses embroidery software to trace the design art. But that’s not the half of it. The digitizer must take multiple factors into account, including:
- Design Size
- Stitch Type
- Stitch Length and Width
- Stitch Angle
- Fabric “Push and Pull”
Stitch Types
All machine embroidery uses three main stitch types. They are:
- Running Stitch (a/k/a Straight Stitch or Walking Stitch)
- Satin Stitch
- Fill Stitch (a/k/a Tatami Stitch)
The most basic is the running stitch, or straight stitch. The other stitch types are variations on this stitch. It’s simply a point-to-point line. It is most often used for outlining, shading and detail work.
With the running stitch, the more point-to-point stitches, the greater the detail. It’s important to balance that with the machine operation. Too many short stitches can create thread breaks that slow the process down. Too many long stitches can result in a loose embroidery that’s prone to snagging.
The satin stitch is used for nearly all text on patches, and also for borders. Similar to a zigzag stitch, it allows high density in small areas. That makes it ideal for text.
Last but not least, is the fill stitch, also known as a tatami stitch. This style is used, as the name implies, to fill in background areas and completely cover the base material with embroidery.
Choosing the right stitch type for every part of the design doesn’t just ensure the best looking patch. It also means the resulting embroidery will be created in the most efficient way possible.
Stitch Length and Width
To make your design look its best, the digitizer must calculate both length and width of each stitch style. As noted above, it’s a balancing act. It’s all about achieving the best blend of stitch type, size, and density.
Patches are most commonly priced for a set number of stiches. If additional stitches beyond that number are required, the price goes up. The goal is to enable the embroidery machine to create the most attractive patches with the minimum possible number of stitches. That saves both production time and thread, giving the buyer the lowest price.
Push and Pull
“Push and pull” refers to how the fabric being embroidered can affect the width of the stitching. The digitizer must compensate for it to avoid designs that are sloppy looking, particularly with text.
After Digitizing
Once the digitizing is done, it’s just a matter of saving the file in the proper format, then downloading it to the embroidery machine. When that’s done, the machine can produce your patches quickly and efficiently. After that, your order gets carefully inspected, packed and shipped to you.
While there’s plenty more to learn about digitizing, now you know the basics of what goes on behind the scenes to create your patches.